How Encoders Work
Let's start off by discussing what an encoder is.
What is a Shaft Encoder?
A Shaft Encoder is an electromechanical transducer, which converts a rotary position into an electronic signal suitable for providing input data to a vast range of electronic control devices.
Shaft Encoders are used for a variety of mechanical applications. The following are just a few examples:
- Measuring the length of raw material during a winding process, then again when the material is cut to size for final use.
- Determining angular positions when synchronising machine movements, such as those found in packaging machines.
- Monitoring the position of products on a conveyor.
- Positioning of indexing tables, stacker cranes, etc.
- Tracking the position of automated robots, and their arm movements.
- Some of the more unusual applications include satellite tracking, road surface analysis and automobile suspension studies.
In 1981 PCA Encoders commenced assembly of incremental encoders in Australia with one body style, that had only two output options. Today, we assemble five body styles.
Each of these is available with a range of shaft sizes, output options, and connecting methods, providing over 3500 different model possibilities. You can browse our range of incremental shaft encoders by clicking on the following link:
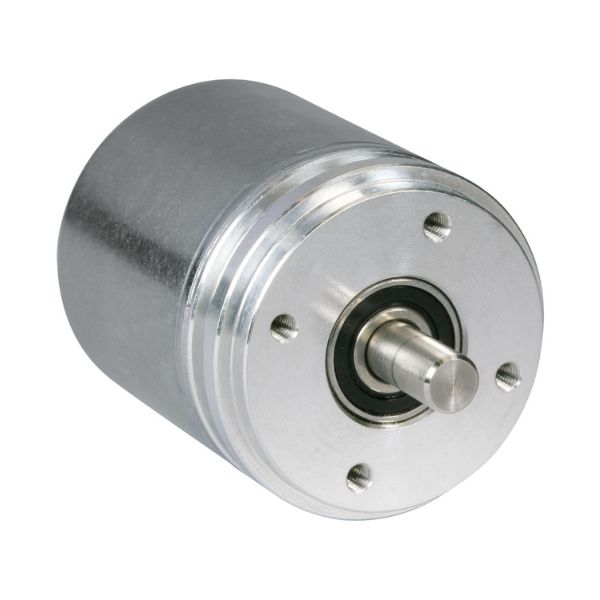
In addition, we have a large library of incremental disks, with increments ranging from 1 to 100,000 per revolution. When we receive an order, the optical disc and output circuit board are assembled into the bearing housing. The completed encoder is normally shipped to the customer within seven days of placing an order. A 24/48 hour build service is also available for those unforseen emergencies.
What is the Difference Between an Incremental Encoder and an Absolute Encoder?
Incremental encoders provide a serial output train of square wave signals as the shaft rotates. To determine the angular position or direction of rotation, external electronic circuitry is required. The number of signals per revolution of the shaft is determined by the customer’s selection when placing an order.
Absolute encoders provide a parallel output structure, the code of which gives a direct reading of the shaft’s angular position, there is an optical reading device for each of the tracks. All disks are formatted with a Gray code; to ensure there are no reading errors, this code has only one bit change between divisions. E-PROMs inside the encoder are used to program the individual output code and add direction.
Incremental Encoder Reading Principle
Most of our encoders are fitted with unique laminated plastic disks, produced with very specialised equipment . These disks have a low mass, excellent shock resistance and can be reproduced economically, making our encoders better suited to harsh environments than those encoders normally using glass or fine metal disks.
As the disk rotates, it interrupts an inferred light path sending signals to a Schmitt Trigger and then to the final output amplifier. Except for very low increment models the light path has a stationary mask or grid with the same increment pattern as the disk. This is known as the Moire‘ Fringe principle. The grid is divided into two halves with a 90° offset between the two, providing the quadrature function essential for direction control.
Incremental Encoders
Incremental encoders are the most common type. They have only one graduated track around the disk perimeter and a serial output pulse train, making them much simpler internally than Absolute encoders, and are therefore a little more economical.
The main point to consider is that the actual shaft position is an assumed relationship between the shaft and associated external counting equipment. If the power is removed it is normally necessary to provide a means of resetting the associated circuitry to a known reference point. Up to three independent optical channels are available in each encoder. In addition the complement of each channel is available, making a total of six output signal lines.
The output signals are referred to as ‘A’, ‘B’ & ‘O’. The ‘A’ & ‘B’ outputs are setup with a 90° offset, commonly referred to as quadrature. Associated counting equipment monitors this relationship and determines the shaft direction. This feature provides up/down information for counters and with the right circuitry prevents incorrect counting in applications where vibration causes problems.
The quadrature relationship in association with external circuitry can also provide the ability to multiply the output signals by four. Thus a 5000 increment model can provide 20,000 increments per revolution.
The ‘O’ output provides one signal for each revolution of the shaft. The signal is used as an exact reference point to coordinate the serial pulse train with a known mechanical location. To use this effectively, it is necessary to install the encoder with a clamp mounting bracket, or some other means that will allow the body of the encoder to be turned.
The state (high or low) of the ‘O’ or output pulse can be selected. However, it is important to note that there is not necessarily any fixed relationship between the edges of the ‘O’ output and the incremental channels. A known relationship can be provided if specified in the part number selected. NOTE: this option is not available for some high increment models.
Absolute Encoders
These encoders have a multiple track gray coded optical disk that has one track for each ‘Bit’ of its stated resolution. This code has the advantage that only one ‘Bit’ changes for each change in output code. The final output code, Gray, Binary or BCD, and the direction of shaft rotation to increment the output value in most models is programmed into E-PROMs.
Each individual increment forms its own unique code on a parallel output bus. Therefore, even if the power fails, once restored, the position of the shaft is immediately known without any resetting routine, as is required with Incremental encoders.
The main consideration is that standard Absolute encoders only provide this feature for one shaft revolution. Therefore their use is restricted to synchronising machinery based on a 360° cycle. If more turns are required it is necessary to use some form of mechanical reduction, or select one of our Multi-Turn Absolute encoders. This type has an internal mechanical arrangement that drives multiple absolute code disks.
Multi-turn absolute encoders are available with resolutions up to 30 bits, this is achieved with a mechanical build that has 14 bit (16,384) turns of the shaft, and 16 bits (65,536) for each shaft revolution. Encoders are available with both parallel and serial outputs; the serial protocols’ are the preferred option today, this approach considerably reduces the field wiring and the I/O ports of the control devices.
Encoders are available with all the most common industrial interfaces, DeviceNET, Ethernet in a number of formats, CanOPEN, InterBUS, ProfiBUS-DP and SSI the simplest of all the protocols. Refer to our web site for full technical details for each interface.
Encoder Output Circuits
In the past there was a range of five different output options, available for some of the series, providing for all types of input structures to which encoders may be connected. Today most of our encoders have the same output driver regardless of the rated voltage. Encoders rated for 5 Volt operation simply have the reverse voltage protection diode removed to ensure that the logic “1” is as close as possible to the + 5 Volt rail.
The maximum output frequency is typically 300kHz, but depends upon the length of the connecting cable, as the line capacitance increases, the rise and fall time of the square waves also increases.
Push Pull
This is now the most widely used output configuration, and will normally operate at any voltage from 11 to 30 Volts. The main feature of this structure is that it can be used to switch either NPN or PNP input circuits, thus reducing spares inventory if both types are required on the one site.
Most of our encoders today are only made with Push Pull output, if a true open collector is required or the output is required to switch a different voltage than the encoder power supply, this can be achieved with one external diode.
NPN or Current Sink
This has a 40mA switching action between the output signal and the 0 Volt supply. Pull up resistors are fitted between the output and the + Volt power supply line.
PNP or Current Source
This has a 40mA switching action between the + Volt supply and the output. Pull down resistors are fitted between the output and the 0 Volt power supply line.
Line Driver
This uses a push pull line driver output circuit which provides a 5 to 15 Volt 40mA output signal capable of driving cable runs up to 100 metres.
This type has the highest frequency response capability and the best noise immunity, provided the installation is equipped with a differential line receiver. To utilise this function output signal options must be selected to provide both the true and compliment signals.
5 Volt Only
The output circuit is essentially the same as the Push Pull circuit shown above, but it has the reverse voltage protection diode removed for 5 Volt TTL operation.
NOTE: The output and voltage information is typical, refer to the individual Series data sheets for specific details about the model you have selected.
PLEASE NOTE: Every effort has been made to ensure the information contained within this blog post is correct at the time of production. However, we have an ongoing development program and upgrades are made. Normally these will have no effect to applications however, current information is always available upon request. Neither PCA nor our prime suppliers accept any responsibility for incorrect use of the product or liability for any damage it may cause to any other part of your equipment.
IS THIS INFORMATION USEFUL?
If so, why not share it with your peers and colleagues. Simply click on the blue LinkedIn share icon below.